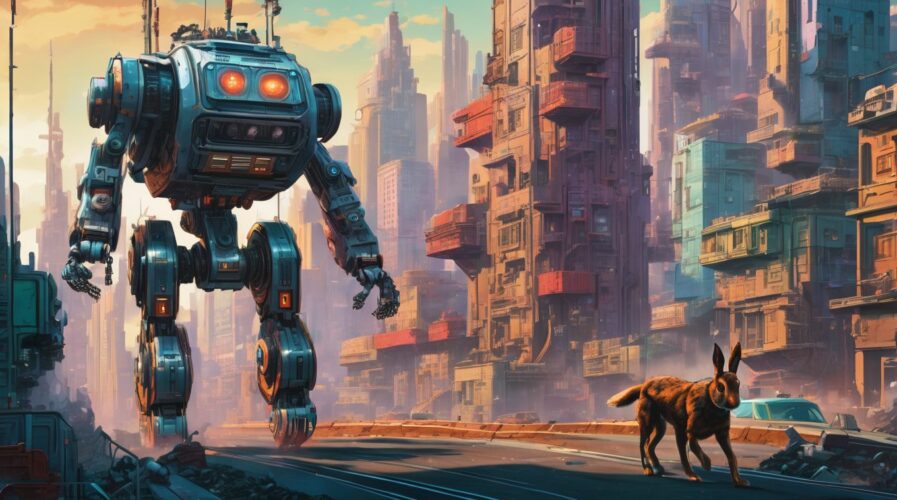
Autonomous robots working (and living?) alongside humans. (Image generated with no sense of irony by AI).
The evolving robot: Past, present and future roles
• Autonomous robots have grown up as capabilities were added.
• New-generation “cobots” are increasingly autonomous.
• As costs come down, the ubiquity of autonomous robots will go up.
Modern society is driven by advancements in technology, including software, electronics, robotics, and more. Every day, we see technology developing, changing the ways we work and do business. At the forefront of current technological progress is arguably the double-act of AI technology and autonomous robots. There is little doubt that mobile, self-governing robots will play key roles in the future.
In just 50 years, the market for industrial robots has evolved significantly. Today, that evolution has delivered “cobots,” otherwise known as collaborative robots that work alongside humans. Whether autonomous robots will continue to work side-by-side with organic people, or take over their roles completely, is a debate that rages on.
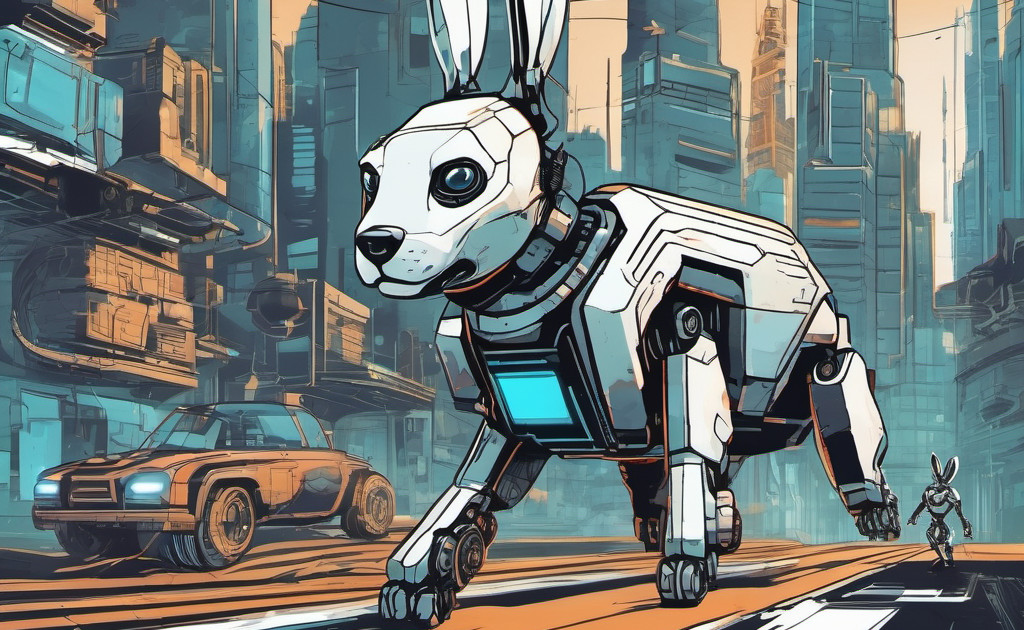
Dawn of the RoboDog. (Image generated by AI).
Artificial intelligence technology has accelerated at an astounding pace over the last two years, affecting many sectors across the globe. AI has become a part of everyday life for so many, with intelligent assistants on hand to support us as we work. They are now at our beck and call, answering queries, and even performing repetitive dull tasks in various industries.
Hasn’t that always been the point of technological advancements, though? To help us complete physical tasks quicker, or even to do them instead of us, freeing human beings up to do more intellectually demanding tasks? If recent decades are anything to go by, we are relying on automation more than ever before.
Emerging as a key competitive factor for manufacturing operations worldwide, the number of industrial robots being used in the workplace has grown exponentially since the 1970s. For instance, only 200 industrial robots were being used in the US in 1970 compared to 4,000 in 1980. By 2015, that number had risen to 1.6 million. Today, there are an estimated 3 million or more autonomous robots in use.
Robots in industry through time
To understand the impact of robots on different industries, we need to go back to their origin in the 1940s and 1950s. British neurophysiologist, W. Grey Walter, was the man who started it all, developing Elmer and Elsie, two robots in the late 1940s. Inspired by biological systems, Grey Walter’s “Tortoises” (as they were also affectionately known as) exhibited fundamental autonomous actions. Using basic sensors, the robots could navigate their surroundings and even respond to stimuli, mirroring lifelike behavior.
During the 1950s, the progression of autonomous technology continued with George Devol, “the Grandfather of Robotics,” creating Unimate. Beginning with basic devices for moving objects autonomously, Devol is credited with inventing the first industrial robot as we understand the term today.
Over time, advancements in electronics, sensors, and software expanded autonomous robot capabilities to include complex tasks like painting, welding, and precision work.
These early examples of robots began being used commercially on assembly lines by the early 1960s, primarily performing heavy lifting tasks – establishing the notion that robots were for tasks that would have been physically difficult for individual average humans to accomplish. But the robots didn’t stay locked into heavy lifting tasks for long. It soon became evident that the robots were significantly increasing manufacturing productivity.
During the late 1960s and early 1970s, demand for automation increased. So industrial robots shifted from mostly heavy lifting to more precision tasks, prompting the development of smaller, electric models equipped with advanced controls and motors that were ideal for assembly work like tightening bolts and nuts. Robots added dull, repetitive work to heavy, difficult work and broadened their repertoire significantly.
Fast-forward to the late 1970s, and robots had expanded their capabilities even further. This included tasks like arc welding, intricate painting, and hazardous environment operations, allowing humans to work on other, less risk-intensive areas of production, while simultaneously raising safety in robot-friendly industries.
This enhancement of workplace safety allowed robots to handle dangerous conditions in environments such as steel mills, freeing skilled laborers to focus on more critical manufacturing operations and ultimately boosting productivity.
Enthusiasm for robotics continued into the mid-1980s. Engineers started to innovate with a view to progressing the industrial landscape faster than ever before. This was the era that sparked the evolution of modern industrial robots, integrating advanced sensors and basic machine vision systems.
As technology continued to advance and computer hardware costs decreased, robotic capabilities took a substantial leap. Engineers were able to install precision force sensors and lasers on robots, allowing them to detect and track components on assembly lines, providing a human-like sense of sight and touch that feels familiar when we look at Amazon’s new robotic solutions, Sequoia and Digit. Like Amazon’s “humanoid” robots, the 1980s’ engineering marvels elevated robots from repetitive task performers to machines that exhibited “limited intelligence.”
While 1980s autonomous robots, otherwise known as autonomous guided vehicles (AGVs), could transport goods and materials from one workstation to another, they still lacked the flexibility and adaptability of the autonomous mobile robots we know today. But, as we stepped into the 1990s and 2000s, there was a rejuvenated interest in the development of true autonomous mobile robots.
That resurgence of interest brought progress in the development of artificial intelligence, sensor technology, and machine learning. Piece by piece, autonomous robots were able to perceive their surroundings more attentively than ever before thanks to advanced sensors. The robots could also learn from their experiences and adapt to changes via newly updated AI algorithms. This was the genuine dawning of the age of autonomous robots.
As the 2000s rolled on, independent robotic system technology began to genuinely excel. Over the last decade or so, mobile autonomous robots have been adopted by numerous industries across the world, including software, manufacturing, retail, and healthcare. While most still work alongside a human workforce, these robots have streamlined warehouse operations and revolutionized the way products and materials are handled.
Yes, these robots have replaced human workers in many environments; something that holds many ethical conundrums for another day. It’s the fact that these robots can augment a human’s capabilities that make them a priceless commodity in various industries. Although there are a host of drawbacks associated with the use of this technology, there is little doubt that autonomous robotic systems have helped improve safety, increase productivity, and introduced new, exciting possibilities in the world of innovative machine learning technology.
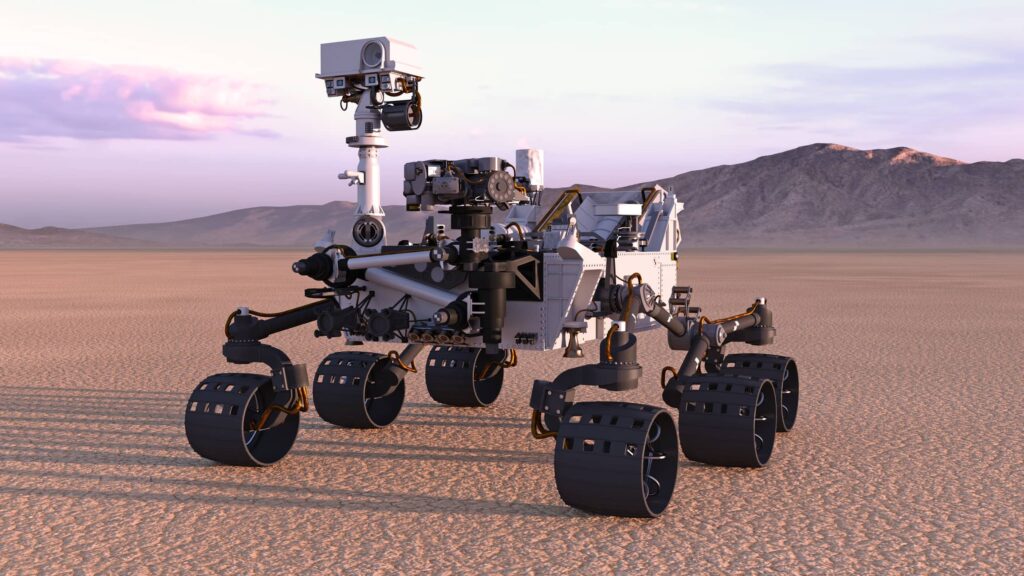
Mars Rover, a space-based autonomous vehicle on a deserted planet.
The present and future of autonomous robotics
Today, mobile autonomous technology is widely used in the industrial sector, as well as sectors like agriculture, health, logistics, and property maintenance. Although adoption on a full scale may still be years away, mobile robots maintain their potential to completely change the way business is done in the future. Even in the modern age, autonomous mobile robots are evolving. That just leaves us with the question of the future of robots in industry.
Today, machine learning and AI has empowered industrial robots to make autonomous decisions without the need for human guidance. Modern robots are able to analyze extensive sets of data, improving their performance via varying mechanical motions. Engineers now prioritize instilling “real intelligence” in robots for increased complexity and efficiency, cultivating a safe collaboration with humans in manufacturing settings.
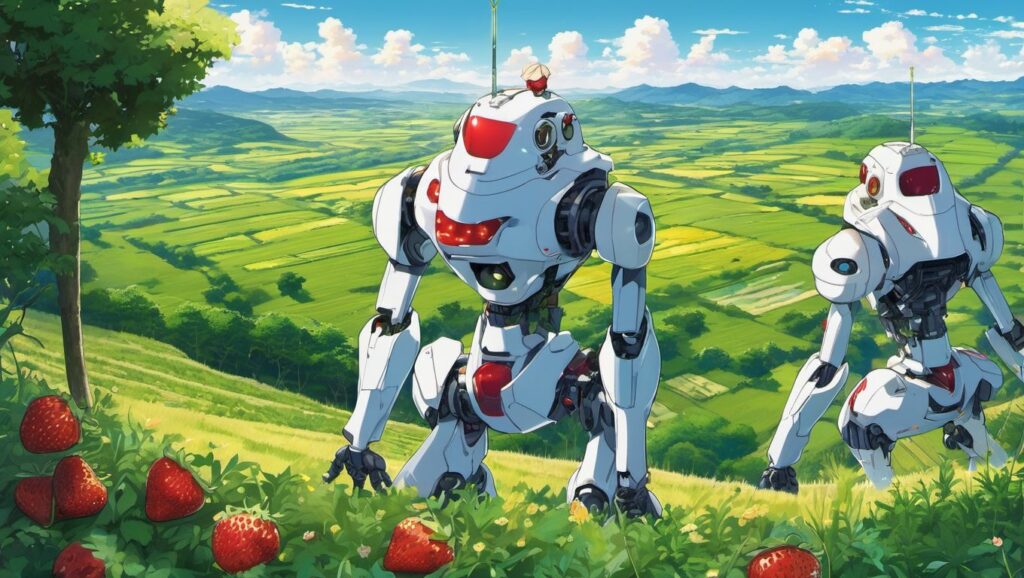
Cyber-strawberry season. (Image generated by AI).
In recent years, there has been a rise of collaborative robots (cobots). This marks a shift towards robots that are designed to operate alongside humans safely. Using force-limited joints and computer vision, cobots can interact directly with humans. But, being smaller and lighter, they are trained to complete specific tasks, freeing up human workers to focus on other jobs.
Initially passive, the development of cobots has been incredibly swift. They now have independent power sources, enabling them to add precise object manipulation and environmental awareness to their bag of capabilities. Their seamless operation alongside human workers has already resulted in mass changes in the manufacturing world, as shown by the nearly $1 billion cobot market and 40,000 operational machines worldwide.
The future of autonomous robots includes a much wider adoption of cobots, particularly ones that will drive efficiency. As costs come down, their wider adoption will make autonomous robots a fact of life across industrial sectors all around the world.
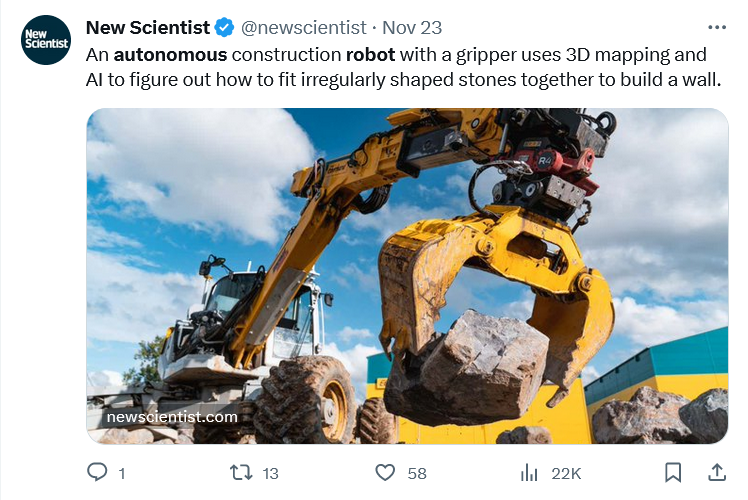
Autonomous robots will soon be in every sphere of our world.
READ MORE
- Data Strategies That Dictate Legacy Overhaul Methods for Established Banks
- Securing Data: A Guide to Navigating Australian Privacy Regulations
- Ethical Threads: Transforming Fashion with Trust and Transparency
- Top 5 Drivers Shaping IT Budgets This Financial Year
- Beyond Connectivity: How Wireless Site Surveys Enhance Tomorrow’s Business Network